国家科学技术奖励大会召开后,央视、新华社等众多媒体对王小谟院士、空警2000进行了更多的补充报道。但人们忽略了“飞机钛合金大型复杂整体构件激光成形技术”这个国家科学技术进步奖一等奖获奖项目。
这个项目应该还属于保密内容,众多媒体报道中只是简略地提了一句,科技部网站的2012年度国家技术发明奖获奖项目目录则压根不予披露,目录里的国家科学技术进步奖一等奖获奖只列了其余2个通用项目。但我们还是可以从公开报道中对该项目有一个基本了解。
早在奖励大会召开前的1月13日,兴业证券公司发布的《机械行业价值周报》就提到,中航重机子公司中航激光王华明团队研发的“3D激光快速成型技术”将获2012年度国家技术发明奖一等奖(这里应是兴业证券将奖项弄错)。有意思的是,证券业界其后普遍质疑兴业报告是操纵股市需要,因为中航重机股价在消息刺激下其后两天连续涨停。
但笔者认为,这一技术的意义价值远远超过中航重机股价上升,对中国先进军机制造的意义是无法用金钱来衡量的。
什么是“飞机钛合金大型复杂整体构件激光成形技术”?或许“3D激光打印技术”会让人更容易明白。该项技术就是通过3D激光打印来制造飞机钛合金大型复杂整体构件。
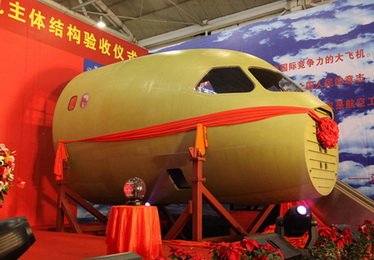
那么什么是“飞机钛合金大型复杂整体构件”?“构件”即是用于承力的飞机结构部件,“整体”即是整体式的,不是焊接或铆接拼接而成的,“复杂”是指该部件三维形状复杂,“钛合金”、“大型”这相信都容易理解。具体讲,“钛合金大型复杂构件”比铝合金构件承力性能好,但加工难度大、造价高,只有高端重型战斗机才有资格采用,如俄罗斯的苏27、中国的歼11、歼20、美国的F-15和F-22,而米格29、歼10、F-16、F-35等知名低端搭配机种都无缘使用。
战斗机的最大型钛合金构件是主翼部位的机身加强框。第三代战斗机苏27、歼11、F-15的机身加强框由于当时工艺所限,由多个小型钛合金部件焊接而成的,承力性能提升仍不够。到第四代战斗机,由于设置有大型机身弹舱,对机身加强框承力性能要求更高,所以美国F-22的机身加强框改为“整体制造”。即是将一整块钛合金先通过锻造工艺,获得更强的承力性能,然后进行切削加工,获得所需的复杂形状。这种整体切削加工使F-22机身加强框承力性能再上一个新台阶。但切削加工对材料浪费是极其严重的,F-22机身加强框毛坯模锻件重达2796千克,而实际成形件重量不足144千克,材料的利用率不到4. 9%。这可是价格昂贵的钛合金,所以F-22战机1亿多美元的单价是有原因的。
但王华明团队通过3D激光打印来制造飞机钛合金大型复杂整体构件,在获得同样性能的同时,可以大幅降低造价。《中国航空报》1月10日刊登了对王华明教授的专访报道。报道中提到,王华明教授通过3D激光打印飞机构件综合力学性能达到或超过钛合金模锻件水平。
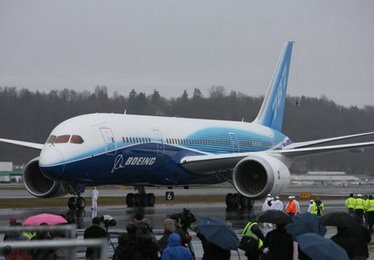
报道提到的技术具体成果有:2005年7月成功实现激光快速成形TA15钛合金飞机角盒、TC4钛合金飞机座椅支座及腹鳍接头等4种飞机钛合金次承力结构件在3种飞机上的装机应用,零件材料利用率提高了5倍、周期缩短了2/3、成本降低了1/2以上;制造出了迄今世界尺寸最大的飞机钛合金大型结构件激光快速成形工程化成套设备,其零件激光融化沉积真空腔尺寸达4000mm×3000mm×2000mm;2009年,王明华团队利用激光快速成形技术制造出我国自主研发的大型客机C919的主风挡窗框,在此之前只有欧洲一家公司能够做,仅每件模具费就高达50万美元,而利用激光快速成形技术制作的零件成本不及模具的1/10;2010年,利用激光直接制造C919达中央翼根肋,传统锻件毛坯重达1607千克,而利用激光成形技术制造的精坯重量仅为136千克,节省了91.5%的材料,并且经过性能测试,其性能比传统锻件还要好。
注意前段所提到的3D激光打印设备的零件激光融化沉积真空腔尺寸,4000mm×3000mm×2000mm的尺寸意味着加工歼20战机的机身加强框已无任何问题。这一技术如果用在歼20战机未来的批量生产上,将有助于降低飞机造价。而中国还在研制运20大型运输机、生产歼11、歼15、歼16重型战机,钛合金3D打印技术都有助于提高它们性能和降低造价。
最近一年来,激光3D打印技术受到了科技界、媒体界的极力追捧。国内还有些媒体提出“3D打印技术剥夺中国世界工厂地位”的担忧。王明华教授团队成果应该可以给予国人更多信心,要求最高的飞机钛合金大型复杂构件,中国人都用激光3D打印技术制造出来了,技术上还有什么需要过分担心的?或许真正的问题在于,如何将这些高端技术在国内制造业推广开来。